The problem of workpiece blackening and molding during aluminum component processing and storage is a major challenge for many aluminum processing industry clients, especially during hot summer days. To address this issue, we need to identify the root causes and apply appropriate solutions.
Problems Encountered During Aluminum Component Processing
01.Material Quality of Aluminum
Cause:
The aluminum components may exhibit blackening or darkening on the surface even before processing, which could be due to excessive iron content in the aluminum material or the use of aluminum produced from recycled scrap. Such aluminum material may not meet the required performance specifications.
Solution:
Select aluminum materials that comply with the standards for processing.
02 .Issues with On-site Mixing Water
Cause:
Harmful ions in water can cause corrosion of aluminum. High electrical conductivity of the water used for mixing can lead to reactions between harmful ions (such as free chlorine) and aluminum alloys, resulting in workpiece blackening.
Solution:
Use purified water (also known as deionized water) or demineralized water (water treated through methods such as distillation, membrane separation, and ion exchange) for mixing to effectively address the electrochemical corrosion caused by water quality on aluminum components.
03.Management Issues with On-site Metalworking Fluids
Cause:
① Improper concentration of metalworking fluids can cause corrosion and blackening of aluminum components.
② Bacteria continuously multiply in the working fluid during the machining process, leading to gradual degradation of the fluid. The degraded working fluid can affect the protective effect on aluminum materials, resulting in workpiece blackening.
Solution:
① Perform regular and scheduled replenishment and replacement of fluids according to operating procedures.
② Regularly monitor the control parameters of the working fluid to ensure that all indicators are within the normal range.
04.Selection of Metalworking Fluids
Cause:
The use of inappropriate metalworking fluids during machining can lead to blackening, molding, and even hairline formation on aluminum components, which indicates corrosion of the aluminum material.
Solution:
It is generally not recommended to use highly alkaline metalworking fluids for aluminum machining. The pH value of the working fluid should be maintained between 8.5 and 9.5. For long machining cycles and high discharge requirements in aluminum processing, emulsion-type metalworking fluids such as SKH®-713, a general-purpose aluminum metalworking fluid produced by Huayang Xinxing Group, are usually chosen. For short machining cycles and low discharge requirements in aluminum processing, synthetic or micro-emulsion-type metalworking fluids, such as SKH®-715N, a general-purpose micro-emulsion metalworking fluid produced by Huayang Xinxing Group, can be selected.
05.Equipment Issues
Problem:
When processing sensitive aluminum alloys, using steel fixtures may cause blackening on one end of the aluminum component due to electrochemical corrosion.
Solution:
Replace the fixtures with aluminum fixtures.
Problems Encountered During Aluminum Component Storage
01.Process-related Issues
Problem:
After aluminum alloy machining processes, if no cleaning is performed to completely remove corrosive substances such as release agents, cutting fluids, saponifying agents, and other stains from the surface of the workpiece, these residues accelerate the formation of mold spots and blackening on aluminum components.
Solution:
Timely clean the machined aluminum components using appropriate cleaning methods.
02.Storage Issues
Problem:
Aluminum components stored under high temperature and high humidity conditions for a long time may blacken and mold due to environmental factors. This is especially true for aluminum components
Solution:
Place aluminum components in dry and well-ventilated areas, avoiding direct contact with the ground to prevent damage to the surface oxide film.
[For Already Blackened Aluminum Components]
Professional aluminum alloy cleaning agents can be used to remove surface mold spots and “black oxide films.” For example, using SKH®-209, a general-purpose metal pickling agent produced by Huayang Xinxing Group, in combination with ultrasonic cleaning or immersion brushing can effectively solve the problem of workpiece blackening and mold spots on aluminum components.
Practical Case Demonstrations
01

The customer has high precision requirements for the workpieces. After using SKH®-713 for aluminum and copper machining, the workpiece surfaces are smooth, flat, and highly precise, with no corrosion. Additionally, it improves the tool life, meeting the customer’s high-standard on-site demands.
02
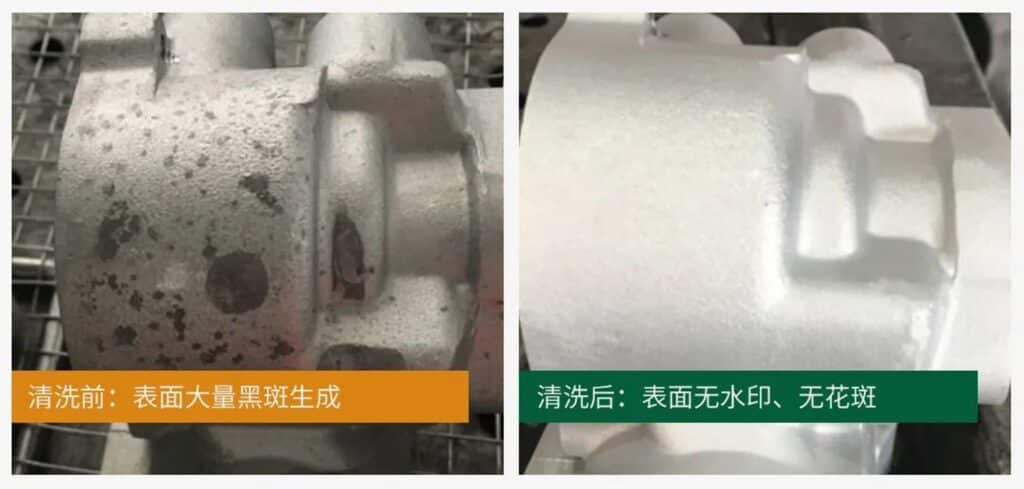
For aluminum castings produced by a certain customer, the surface of the cast aluminum parts developed black spots during storage due to local production environment factors (high temperature and humidity). The black spots on the surface needed to be removed before assembly.
The customer used SKH®-209 in combination with an ultrasonic cleaning process to remove the black spots on the workpiece surface. After the cleaning process, the workpieces were dried with high-pressure air, resulting in a surface free of watermarks and blemishes, meeting the customer’s requirements.”